Photoelectric sensors
Photoelectric sensors detect the presence of objects based on the reflection or interruption of the emitted light beam. Distance sensors can also detect the exact distance using the principle of ToF measurement. They can detect non-transparent objects & levels of turbid liquids at high ranges w/o contact. Read more here




Optical measurement technology – (almost) all in using photoelectric sensors
How photoelectric sensors work
Basically speaking, all photoelectric sensors in industrial environments work according to the same functional principle. Light (whether laser or red light is irrelevant at this point) is emitted by an emitting element and detected by a receiving element. The transmitter and receiver elements are usually located in the same component, the sensor head. When an object is detected, the sensor either issues a switching signal or a distance value.Types of photoelectric sensors
Generally, photoelectric sensors can be divided into the following four sensor groups:- Diffuse reflection sensor
- Retro-reflective sensors
- Through beam sensors
- Laser distance sensors
- Photoelectric fork sensors
- Colour sensors
- Contrast sensors
Difference between light barrier, light scanner and distance sensor
Light scanners and light barriers are used for the detection of objects. They issue a switching signal if presence of a product is detected in the detection range. By contrast, distance sensors measure the distance to an object and deliver an analogue signal.
With a light barrier the receiver is permanently irradiated by the transmitter. If the light barrier is blocked by an element, the light barrier issues a switching signal. The system switches if the receiver does not detect light from the transmitter. This means that a light barrier is dark switching.
A light scanner works exactly opposite to the way a light barrier does. The transmitter emits a light signal without a ‘specific target’. If the light hits an object, it is reflected at the surface. The receiver unit detects the reflected light and outputs a switching signal. This procedure is referred to as light switching.
The designations light or dark switching are related to the terms NO and NC from sensor technology. They are predominantly used for optical sensor systems. Learn more about normally closed and normally open contacts here. autosen also offers photoelectric sensors the switching function of which can be programmed (light or dark switching). The sensors can also be used as NO or NC contacts.

Comparison of optoelectronic systems
Photoelectric sensors: Advantages and disadvantages
Selecting the appropriate photoelectric sensor
In this section you will learn how to select the appropriate sensor for your application, which criteria are relevant, and what stands for or against the individual types of optical proximity sensors.Photoelectric sensor vs. laser: Sensor with red light, infrared light or laser light?
Red light, infrared light or laser light? Where are the differences, advantages and areas of application?
Red light offers easy alignment of the optoelectronic sensor as the light spot is relatively large and easy to detect. Retro-reflective sensors with red light are easy to install as they need not be aligned ultra precisely thanks to their great cone of light.
Infrared light is invisible to the naked eye, as the wavelengths of infrared light are not within the visible spectrum. This makes alignment of the sensors more difficult. The great advantage of infrared light is that dark and black surfaces can also be detected with large ranges.
Sensors from autosen using laser light for measuring emit the laser beam in bundled and very short pulses. This results in high laser intensity and large ranges. Due to its small diameter, the focused laser spot is particularly suitable for detection small objects such as threads.
Which photoelectric sensor is the right one for your application?
Diffuse reflection sensors, retro-reflective sensors and through beam sensors detect objects reliably and provide a binary switching signal. Laser distance sensors precisely measure the distance and output the distance value as an analogue signal. Additional advantages are:
Diffuse reflection sensors:
Space saving and easy to install, as the transmitter and receiver are located in one device. Problematic when used with poorly reflecting surfaces. Background suppression is necessary if the emitted light is reflected behind the measuring range.
Retro-reflective sensor:
The range is independent of the object and the measuring principle works with both opaque and reflective surfaces. A reflector is required.
Through beam sensor:
Similar advantages as for the retro-reflective sensor, has greater ranges and is less sensitive to interferences under aggravated conditions, e.g. dust-laden air. Elaborate installation, as the transmitter and receiver require a voltage supply.
Photoelectric fork sensors:
Small range with very good sensing of small products regardless of the degree of reflection and colour. Simple installation as transmitter and receiver are located in a compact housing.
Laser distance sensors:
The high intensity of the light beam enables distance measurements over a large range. The focused laser beam enables the reliable detection of very small objects.
Colour sensors:
Reliably detects colour shades of objects and is also used for detection, sorting and control of objects by their colour, and also in fast processes with great numbers of items.
Contrast sensors:
Detects grayscales with the aid of red, green and blue light and detects pressure marks and contrasts as well as the smallest differences in brightness for grayscales and colours.

Red light, infrared light or laser light? – You decide!
We offer our optical diffuse reflection sensors, retro-reflective sensors and through beam sensors as red light, infrared light and laser variants. We provide the full-scale portfolio. Utilise the benefits of the different optoelectronic sensor systems. Distance measurement is available in the laser version only.
Stainless steel or plastic housing? – You decide!
Our new, ultra-compact photoelectric sensors are now available with two particularly advantageous housing materials: with an ultra-compact stainless steel housing featuring protection rating classes IP65, IP67, IP68 and IP69k for application in wet zones, or as an extremely robust plastic version for use in demanding standard applications.
Photoelectric level sensors
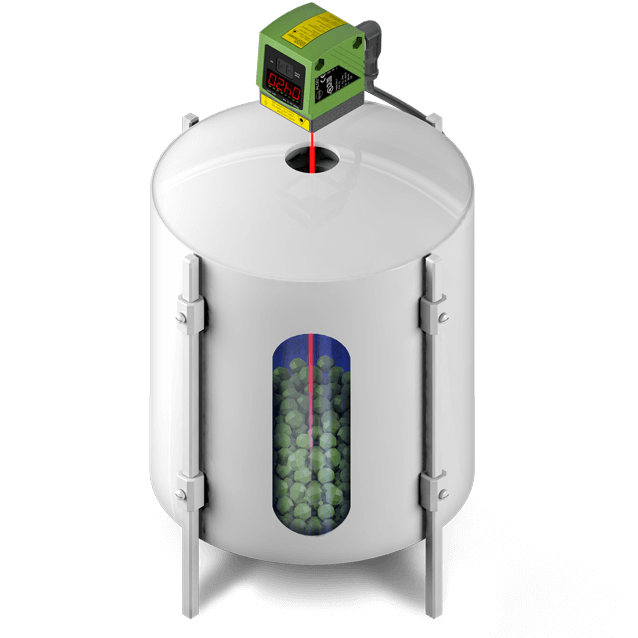
The photoelectric sensors are suitable also for measurement of continuous levels (for example AL001-004). They detect great distances up to 10m without contacting the medium and are appropriate for level measuring of opaque liquids and bulk materials.