Jaspers - High-end sensor technology by candlelight

A shining example of simple digitisation
Sensor-to-cloud applications make production processes efficient, secure and transparent. The Karl Jaspers Candle Factory in Paderborn, Germany, shows how this can be achieved step by step with simple means. The company has begun to gradually digitise its own machinery with the autosen io-key.
Automation whenever possible, manual labour whenever necessary – according to this motto, the Karl Jaspers Candle Factory has developed over the past 100 years into one of the few internationally successful candlemakers in Germany. Today, production capacities are over 20,000 tons of paraffin wax a year. The assortment ranges from tea lights to scented candles and church candles, a speciality of this renowned company. Candles are supplied to trade customers, the catering sector and churches.
Public holidays, the outdoor season and the Christmas period cause rapidly changing high-demand peaks for the various types of products. In addition, colour, shape and fragrance trends are continuously changing at ever faster rates. The machines must therefore run reliably and allow quick changeover. Furthermore, depending on the actual product, various production requirements must be adhered to precisely, for example with regard to the temperature of the paraffin, in order to ensure high quality. Candle manufacturing is not just traditional craftsmanship but also a high-tech procedure that requires a high level of logistics performance.

The plug & play concept demands neither programming effort nor any other modification of the existing IT infrastructure.
Thomas Jaspers, Managing Director

A question of resources
Today, well over 90% of the production steps at the plant in Paderborn are already automated, and digitisation is therefore the next logical step. To do so, the company was looking for a simple and uncomplicated solution. This should enable efficient, step-by-step entry into what managing director Thomas Jaspers would call “Skilled Crafts 4.0” – digital fabrication in which skilled manual values are not lost. A main challenge: It should be possible to monitor system conditions at any time via sensor data in the cloud. There was neither an independent cloud environment nor – apart from the tech-savvy management – any programmers, IT or sensor experts.
Choice fell on the recently launched autosen io-key. This complete system has been specifically designed for users looking for a risk-free and cost-effective way to digitise, regardless of the industry or company size. The io-key consists of a gateway, which combines sensor data and transmits it at required intervals, an integrated SIM card for data transmission and a high-performance cloud environment. The plug & play concept demands neither programming effort nor any other modification of the existing IT infrastructure. Set-up of the io-key is simple and does not require any specialist knowledge; “it can therefore be carried out in a short space of time by the employees on site,” explains Jaspers, who also aims to make better use of staff resources through digitisation – keyword “lack of skilled workers”.
Critical areas as a test environment
Jaspers initially installed the io-key for test monitoring of the quality-critical temperature in paraffin, the raw material for candles. Deviations from the ideal values and tolerances, which vary from recipe to recipe, can lead, for example, to colour defects or other production problems. If they are not detected in time, entire batches are quickly lost. The existing temperature sensor could only be read out locally, meaning regular on-site machine inspections were previously necessary. The company therefore required a new solution that transfers temperature values to the cloud at regular intervals and triggers an alarm if limit values are exceeded.
The io-key was installed in the paraffin basin in just a few steps. It was initially wired to the mains via the 24V connection and connected to the IO-Link temperature sensor. In this case the sensor was also an autosen product, but the system basically works with all IO-Link sensors irrespective of the manufacturer – currently more than 6,000 sensors from over 200 manufacturers. The system automatically detects the sensors, the measuring principle and the measured variable via the IODD file. Based on this information, a corresponding visualisation is generated fully automatically. This also applied to the test application: After logging into the autosen.cloud, a customised dashboard was already available for Jaspers Candle Factory in which the current temperatures were visualised on a Celsius display. “It took less than a minute from connection of the sensors to visualisation on the dashboard,” says Jaspers. A few clicks later and email and text notification had also been activated for limit value exceedance. “If we had implemented this alarm function via the machine PLC, for example, a programmer would have had to modify an existing, licensed system and set up new interfaces. However, it would have been difficult to justify the outlay for this provision,” claims the managing director.
In addition to visualisation and notification when limit values are exceeded, the autosen.cloud also offers export options and an archive function. Further, historical data is also available in the review. In other words, the entire production chain or a quality-critical section can be documented. If, for example, there are discrepancies regarding the colour of the candle, objective data can be used to determine whether there was a temperature delta during production of the corresponding batch – also using a mobile device directly at the customer’s production facility. Jaspers: “This strengthens customer loyalty and enhances the confidence of partners in our production skills.”
Gradual expansion
Following the successful io-key test, the plan is to also use the system in other areas of candle production. In principle, new devices are not even required for further test operation: The io-key is not coupled to a specific machine and as such can be used for various operational applications as required – regardless of the measuring principle. If the tests are deemed successful, the system can be expanded as and when necessary with additional devices, each designed for two sensors. They can all be monitored on the same dashboard. Current plans include deployment at the company’s own wells and heating systems, but also along with vibration sensors in the forklifts to detect possible collisions. The aim is to combine the available sensor data at a central point, thereby providing the company and production management with a comprehensive overview of all plant processes and conditions. “A scenario that would not have been realistic for us in this form any time soon with conventional devices,” explains Jaspers. “The io-key allows us to replace the island solutions at the machines and further expand our core competence in candle production compared to our competitors.”



io-key connected and mounted with power supply and sensor cable.
Everything at a glance
The candle manufacturer Karl Jaspers GmbH from Paderborn uses autosen's io-key for step-by-step digitalisation of its machinery.
With over 90% of its production steps automated, the company's goal is a simple and economical digitalisation solution for monitoring the plant conditions via sensor data in the cloud.
The io-key enables monitoring of the paraffin temperature, a quality-critical area that helps avoid production defects.
After successfully testing the io-key, the factory plans to use the system in other areas of candle production, thereby optimising its production processes.

Production, wholesale trade and retail trade as well as distribution of/with candles
Kerzenfabrik Karl Jaspers GmbH
Eggertstraße 24, 33100 Paderborn
verkauf(at)jaspers(dot)de
+49 5251 52400
www.jaspers.de
Products used
More success stories
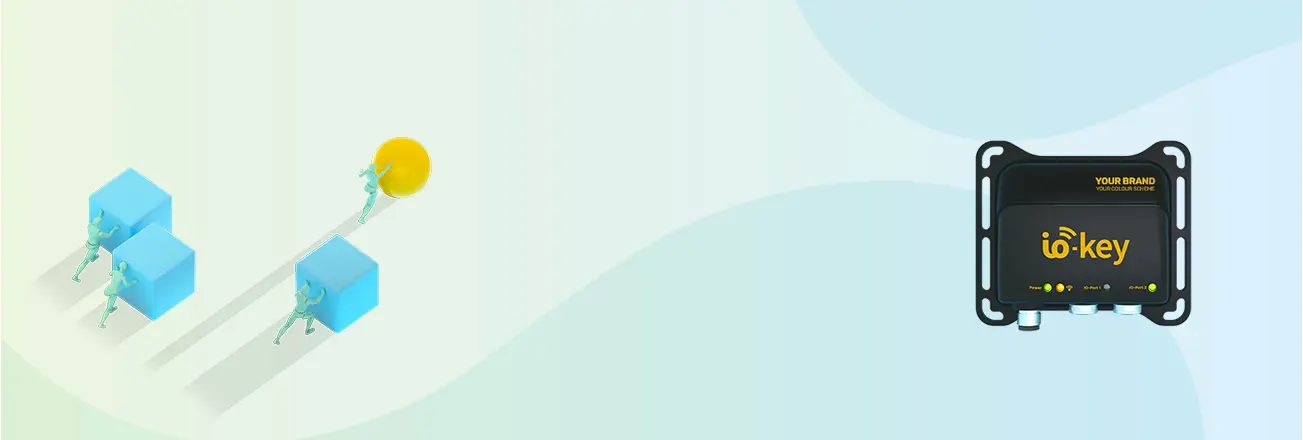
Get your business idea off the ground with the io-key® whitelabel packages. to get your business idea rolling!
Learn more