
Inductive sensors
Inductive sensors are non-contact sensors designed to detect (conductive) metal objects. They use a magnetic field that is generated at the front of the sensor. A metal object dampens this magnetic field and reduces the amplitude of the internal resonant circuit. Once the switching threshold is reached, the sensor emits a switching signal Read more here

50+ in stock!
Online -5,5 %
48.92 €
46.23 €
Back in stock soon
Online -5,5 %
12.70 €
12.00 €
Back in stock soon
Online -5,5 %
12.70 €
12.00 €
Back in stock soon
Online -5,5 %
12.70 €
12.00 €
Mode of operation of inductive sensors
How do inductive sensors work?
Inductive sensors are contactless sensors designed for the detection of (conductive) metal objects. How they work: Inductive sensors operate on the basis of a magnetic field that is generated at the front of the sensor in an open magnetic circuit. The detection principle is based on the damping (attenuation) of the magnetic field by the approaching metal object. The amplitude of the internal resonant circuit is reduced by damping until a threshold is achieved and the sensor outputs a switching signal.
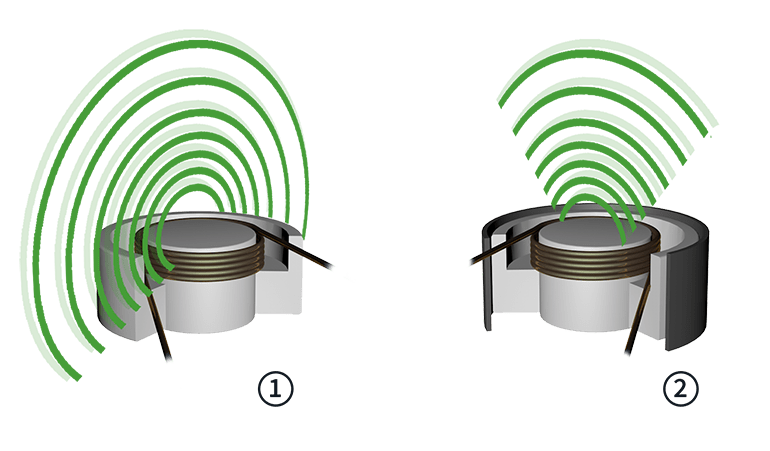
The functional principle
The principle of inductive sensor technology is based on an electromagnetic alternating field created via a copper coil embedded in an open pot core made of ferrite. An resonant circuit is created using the capacitor. An electrically conductive metal located within a certain range in front of the sensor causes strong attenuation of the eddy currents of the magnetic field. These changes in the oscillation amplitude are detected by the sensor and the sensor is switched. The special feature of sensors which can be installed flush is the additional outer metal ring which surrounds the coil. This shields the alternating field and bundles it at the front.
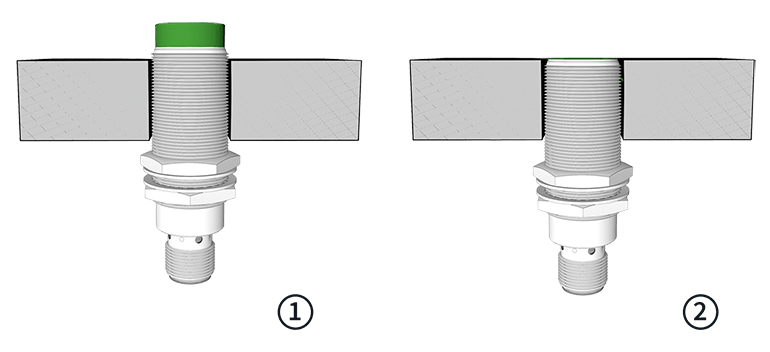

1. Sensor not flush mounted, 2. Flush mountable sensor
a. Metal
Observance of free zones
Free zones refer to areas around the sensor which must be kept free of metallic materials in order not to compromise with the operating principle of the device. With inductive sensors a distance of at least three times the nominal sensing range must be maintained between a metallic material and the sensing face. The correct installation of sensors for non-flush mounting also requires that there is no interference material within a displacement less than the diameter of the detection face.

D: Diameter of the active surface (see data sheet)
1. Sensor not flush mounted, 2. Flush mountable sensor
The sensing range of inductive sensors
The distance at which inductive sensors switch is referred to as the sensing range. Depending on the approaching metal, a correction factor must be applied for the majority of inductive sensors to reduce the sensing range. The following table displays the factors of various metals for the majority of inductive sensors:For some time now, Factor 1 sensors have been available that offer an identical sensing range for all metals (Factor 1). The switching frequency of inductive sensors usually ranges between several hundred and several thousand switching operations per second. Inductive sensors therefore have a very fast reaction time and can be used for speed monitoring, for instance.
Inductive sensors are a type of position sensor. These sensors come into play where it is necessary to register the position of a metallic object within a range of a few millimetres to several centimetres. The actual registration range depends on the sensor model. In almost all automated processes, sensors are essential to provide the control unit with information. Inductive proximity sensors from autosen provide the necessary signals on positions and end positions and serve as a pulse generator for counting tasks or rotational speed registration. The inductive sensors are used in very varied applications with differing requirements regarding the range and protection rating.
Inductive sensors are a type of position sensor. These sensors come into play where it is necessary to register the position of a metallic object within a range of a few millimetres to several centimetres. The actual registration range depends on the sensor model. In almost all automated processes, sensors are essential to provide the control unit with information. Inductive proximity sensors from autosen provide the necessary signals on positions and end positions and serve as a pulse generator for counting tasks or rotational speed registration. The inductive sensors are used in very varied applications with differing requirements regarding the range and protection rating.
Our inductive sensor classes
Standard Class
Inductive sensors of autosen’s Standard Class can be used for all standard applications without particularly challenging environmental conditions and they offer the best price/performance ratio in factory automation.
High Resistance Class
Inductive sensors of autosen’s High Resistance Class are robust and reliable, have a broad operating temperature range and thanks to the high protection rating of up to IP69k they can also be used for more demanding applications, including difficult industrial environments.
Full-metal housing
In addition, autosen supplies inductive sensors with full-metal housings that are specially robust on account of their metal sensing faces. They have been optimized for use in the foodstuffs industry and in wet zones, so they are well able to meet the special requirements that apply in such environments. Inductive sensors with full-metal housings also withstand frequent cleaning procedures and fluctuating temperatures well.
Factor-1 sensors
Our inductive Factor-1 sensors are the problem solvers for almost all applications. They have the same sensing range for all metals (correction factor = 1 for all metals). They can also be used in challenging conditions because of the high protection rating of IP69k. The Factor-1 sensors are resistant to oils and lubricants and provide for a high degree of plant availability thanks to the high switching frequency.
IO-Link
Our inductive sensors with IO-Link can be configured and operated with an IO-Link master. Configurations such as normally open/ normally closed, p/n switching and many more can be set to your requirements and permanently stored. The sensor can even transmit the measured distance and diagnostic data via IO-Link. If you do not use IO-Link, the sensor can be used classically as a proximity switch.
Miniature
Our inductive miniature sensors in cylindrical design Ø3 mm, Ø4 mm, M5 & Ø6.5 mm are particularly suitable for applications with limited space. They are therefore ideally suited for handling technology, robotics and many other applications with limited space.
Inductive or capacitive sensors
They are ideally suited for position detection of metallic objects and small measuring ranges in the range of a few millimeters up to the two-digit centimeter range. However, inductive sensors are not suitable for detecting the position of non-metallic objects or when a longer range is required. In this case, capacitive sensors should be used, which detect objects in small measuring ranges independent of material and surface properties. If longer ranges are required, it is recommended to use ultrasonic sensors, which can also work with all materials and surface conditions, or optical sensors for non-transparent objects.
Advantages and disadvantages of inductive sensors
In comparison with mechanical sensors, inductive sensors have several advantages:
- high switching frequencies
- a specially high degree of switch point accuracy
- and wear-free, contactless operation for registering all kinds of metal
Inductive sensors are ideally suited for use in harsh industrial environments:
- they can withstand dust, moisture and vibrations
- function without contact and wear-free and
- still work properly even if the sensing face gets covered with material
Inductive sensors function consistently and reliably whether registering moving or stationary objects.
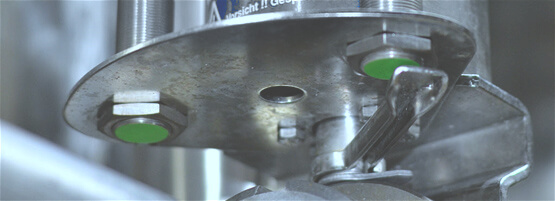

All the advantages of inductive sensors at a glance:
- Reliable position detection for metallic objects and short measurement ranges
- Contactless and wear-free operation
- Exact measurement whether the object is moving or not
- Insensitive to deposition on the sensing face
- Insensitive to dust, moisture and vibrations
- Broad operating temperature range
- High protection ratings
- High switching frequencies and high switch point accuracy
- Higher sensing ranges
- Short-circuit proof and proof against reverse polarity
Application examples for inductive sensors
In view of the many different types, inductive sensors can be used in a very wide range of applications and sectors. Their high protection ratings and robustness make them suitable for use in the foodstuffs industry, beverages industry and robotics.
Here are some examples:
- Detection of moving machine components and objects that are to be processed
- Counting metallic components in component feeding and conveying technology
- Highly precise referencing of zero positions for moving parts (robotics)
- Position monitoring
- Stable drives
- Machine tools
- Hydraulic aggregates
- and much more