Overview
- can be used for measuring vibrations and temperatures at rotating machines
- Sensor preset according to ISO 10816 and immediately ready for use; parameterisation only via IO-Link
- Enables early detection of mechanical impact, mechanical friction and component fatigue to efficiently plan maintenance operations and prevent machine damage and unwanted downtime
- records temperature, v-RMS (component fatigue), a-RMS (mechanical friction), a-Peak (mechanical impact) and the crest factor
- 2x normally closed (NC)

Industry 4.0 & IIoT
Discover a universe of new possibilities with smart solutions from autosen
Discover nowDescription
The AV102 vibration sensor is used to measure vibrations and temperatures on rotating machinery, e.g. pumps, fans, motors, etc. The sensor is preset for large machines (output: > 300 kW; speed 120…600 rpm) according to standard ISO 10816 and ready for immediate use. The compact and robust stainless steel housing with high mechanical overload protection and protection rating IP69K enables safe use in almost all industrial environments.The AV102 allows the early detection of mechanical impact, mechanical friction and component fatigue, enabling the efficient planning of maintenance procedures. This effectively prevents damage to the machine and unwanted downtime - saving both time and money.
The vibration sensor with IO-Link records many process values such as temperature, v-RMS (component fatigue), a-RMS (mechanical friction), a-Peak (mechanical impact) and the crest factor. All process values can be transmitted simultaneously via IO-Link interface, thereby enabling comprehensive machine diagnostics. In the event of damage, raw data can be transmitted via BLOB Transfer using IO-Link.
If IO-Link is not used, the sensor is operated in so-called SIO mode. The factory-set sensor has two switching outputs: OUT1 indicates component fatigue (e.g. imbalance, misalignment) / OUT2 signals mechanical friction (e.g. wear, lubricant problems). Both switching outputs can be configured prior to commissioning via IO-Link parameterisation and output one of the process variables listed above.
If you have any questions about parameterising the IO-Link or you would like to use autosen’s parameterisation service, please contact us. Or get going straight away with the IO-Link Starterkit ADS01.
Technical data AV102
General information
Schwingungsüberwachung an große Maschinen: Leistung > 300 kW, Drehzahl 120 ... 600 U/min
2 ... 10000 Hz
0 ... 45 mm/s (RMS)
1
-30°C ...80 °C (only IO-Link)
Vibration (Veff / aPeak); hysteresis / window; switch points; switching logic; fault indication; self-test; frequency filter
2 ... 10000 Hz
0 ... 45 mm/s (RMS)
1
-30°C ...80 °C (only IO-Link)
Vibration (Veff / aPeak); hysteresis / window; switch points; switching logic; fault indication; self-test; frequency filter
Outputs / inputs
2x Normally closed (NC)
Normally open/ normally closed parameterisable via IO-Link
Yes
Normally open/ normally closed parameterisable via IO-Link
Yes
Electrical data
10 ... 30 V DC
Direct voltage (DC)
PNP
NPN*
*IO-Link parameterisation
100 mA
2 V
250 mA
III
Yes
Yes
Yes
Direct voltage (DC)
PNP
NPN*
*IO-Link parameterisation
100 mA
2 V
250 mA
III
Yes
Yes
Yes
Mechanical data
Threaded pin
V4A (1.4404)
IP67
IP68
IP69k
M12
4-pin
Contacts gold-plated
V4A (1.4404)
IP67
IP68
IP69k
M12
4-pin
Contacts gold-plated
Accuracy
< 2 %
± 2.5 K + (0.2 x (ambient temperature - surface temperature))
< 4 kHz ±10 %; < 10 kHz < 3 dB
± 2.5 K + (0.2 x (ambient temperature - surface temperature))
< 4 kHz ±10 %; < 10 kHz < 3 dB
Ambient conditions
-30 °C
80 °C
80 °C
Additional information
299 years
No
2 threaded pins
DIN EN 61000-6-2
DIN EN 61000-6-3
DIN EN 50178
DIN EN 60068-2-27
DIN EN 60068-2-6
CE
cULus
No
2 threaded pins
DIN EN 61000-6-2
DIN EN 61000-6-3
DIN EN 50178
DIN EN 60068-2-27
DIN EN 60068-2-6
CE
cULus
Drawings
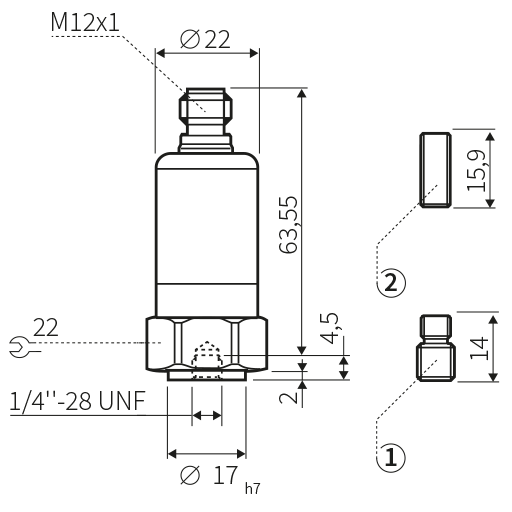
Tightening torque 8 Nm
1: Threaded adapter 1/4"-28 UNF / M8 x 1.25 mm
2: Threaded adapter 1/4"-28 UNF / Tightening torque 8 Nm
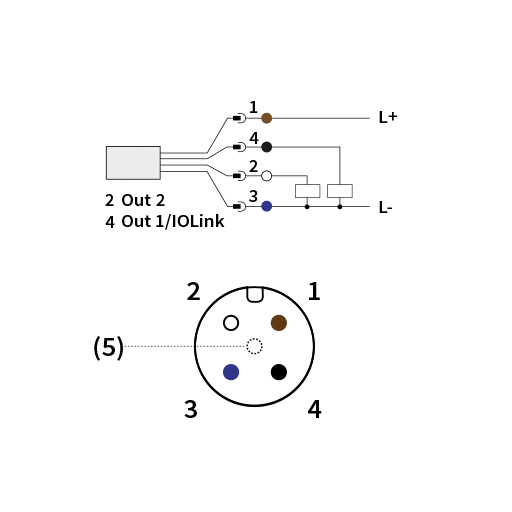
OUT1: v-RMS detects overload (e.g. unbalance, allignment errors)
OUT2: a-RMS detects contact of machine components (e.g. wear, problems with lubricants)
Downloads
Data sheet Customer reviews