Sensing ranges of position sensors
How is the sensing range of sensors defined?
Definition: The sensing range of position sensors is the displacement between the sensing face of the sensor and the approaching measurement object that triggers a signal change in the sensor. The sensing ranges for inductive sensors are determined with the aid of a square of steel (Fe 37), a so-called standard target according to DIN EN 60947-5-2. As a rule of thumb, the larger the sensor diameter, the larger the sensing range. For measurement objects made of other materials, a correction factor must be used in determining the sensing range. The sensing range is also dependent on the size of the measurement object. As a rule of thumb, at least the forward surface of the sensor must be covered in order to reach the sensing ranges as given in the data sheet. If the objects to be tested are smaller, this reduces the sensing range or even renders the object unmeasurable.
How they work
Inductive sensors operate on the basis of a magnetic field that is generated at the front of the sensor in an open magnetic circuit. The detection principle is based on the damping (attenuation) of the magnetic field by the approaching metal object. The amplitude of the internal resonant circuit is reduced by damping until a threshold is achieved and the sensor outputs a switching signal. The distance at which inductive sensors switch is referred to as the sensing range. Depending on the approaching metal, a correction factor must be applied for the majority of inductive sensors to reduce the sensing range. The following figure displays the factors of various metals for the majority of inductive sensors:
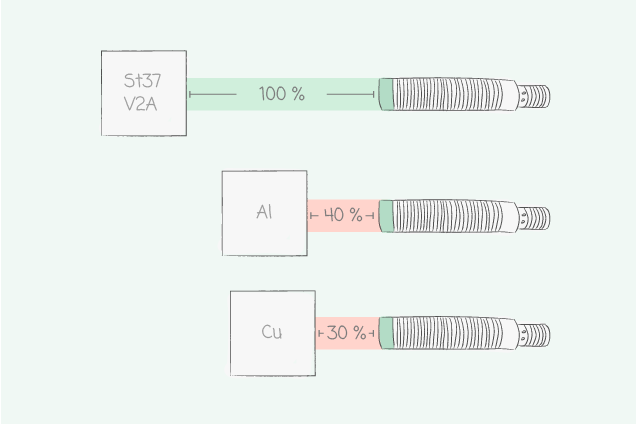
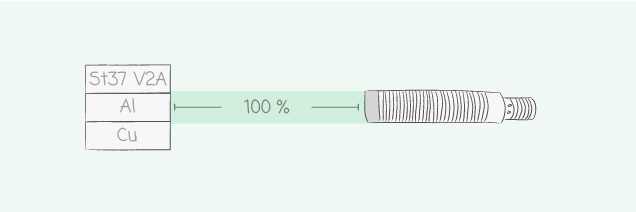

The sensing range of position sensors is the distance between the sensing face of the sensor and the approaching measurement object.
Patrick Targonski, Product Manager at autosen


Manufacturers specify up to four different basic types of sensing range:
- Sn: nominal sensing range or rated sensing range
- Sr: real sensing range
Sn: nominal sensing range or rated sensing range
- Su: useful sensing range
- Sa: operating distance or assured sensing range
Sr: real sensing range
This can be expressed as follows:
Sn * 0,9 ≤ Sr ≤ Sn * 1,1
Su: useful sensing range
This can be expressed as follows:
Sn * 0,81 ≤ Su ≤ Sn * 1,21
Sa: operating distance or assured sensing range
The following definition is applied:
Sa ≤ Sn * 0,8